Konsortialleiter Dr. Falk Eckert zog positive Bilanz: „Am Beispiel des „Digitalisierten Asset Management“ konnten wir eindrucksvoll die technologische Basis einer herstellerübergreifenden und einheitlichen Datenbereitstellung im Datenraum Antrieb 4.0 zeigen. Besonders für KMUs wurde deutlich, wie niedrigschwellig der Einstieg in das multilaterale Datenteilen sein und die Industrie von mehr Effizienz, Zeit- und Kosteneinsparungen profitieren kann.“
In den zahlreichen Gesprächen wurde klar, dass ein gemeinsamer Standard benötigt wird, um die nahtlose Übertragung von Daten und Informationen herstellerübergreifend zu ermöglichen. Antrieb 4.0 zeigte dafür die Möglichkeiten der horizontalen Vernetzung zwischen Antrieben unterschiedlicher Hersteller an verschiedenen Standorten und Produktionsanlagen sowie der vertikalen Vernetzung vom Antrieb in den Datenraum auf.
Am Stand des ZVEI e.V. präsentierte das Forschungsprojekt am Beispiel des „Digitalisierten Asset Management“, wie durch den einfachen Zugriff auf der in einer Anlage verbauten Antriebe und Komponenten im laufenden Betrieb mehr Transparenz in der Fabrikhalle hergestellt werden kann.
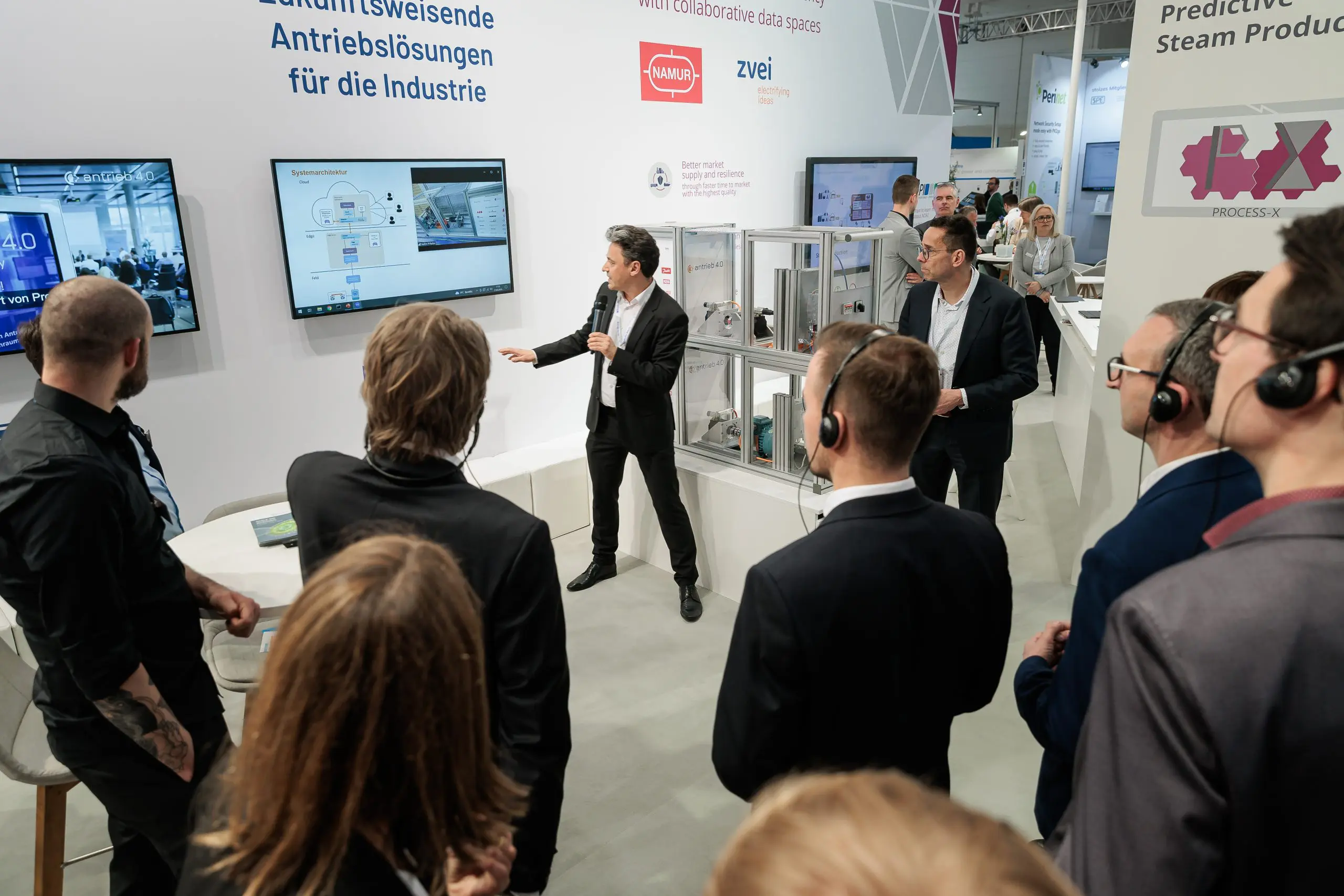
Zeit und Kosten reduzieren, Energie und Ressourcenverbrauch optimieren
Produktionsanlagen sind komplexe Systeme, die sich aus einer Vielzahl von Einzelantrieben und anderen Baugruppen zusammensetzen. Entsprechend umfassend fällt dabei die Anlagendokumentation aus. Während des laufenden Betriebs fallen eine Reihe an Informationen an, die heutzutage in herstellerspezifischen Systemen und unterschiedlichen Formaten bereitgestellt werden. Dies führt zu Informationsasymmetrien bei Entscheidungsfindern und hat unter anderem zur Folge, dass Unternehmen den Betrieb und den Energieverbrauch einer Anlage nicht zielgerichtet optimieren können.
Mit Hilfe des „Digitalisierten Asset Managements“ konnte eindrucksvoll präsentiert werden, wie beispielsweise der Maschinenbetreiber den Aufbau seiner Anlage transparent visualisieren und einen zentralen standardisierten Zugriff auf alle relevanten Informationen bekommen kann. Durch die übersichtliche Überwachung des Zustands und des Energieverbrauchs können damit zukünftig Stillstandzeiten reduziert, der Betrieb optimiert und Kosten eingespart werden.
Für den Antriebshersteller oder den Maschinen- und Anlagenbauer ergibt sich der große Vorteil, spezifisch auf die Anforderungen seiner Kunden eingehen zu können. Während der Antriebshersteller qualitativ hochwertige sowie energiesparsame Komponenten zu marktgerechten Preisen anbieten möchte, baut der Maschinen- und Anlagenbauer entsprechende Anlagen nach den Bedürfnissen des Auftragsgebers. Die Entwicklung erfolgt derzeit auf Basis von Erfahrungswerten, aufwendigen Simulationen, langfristigen und kostenintensiven Tests und Prototypenentwicklungen. Komponenten werden hierbei häufig überdimensioniert. Hier können belastbare Daten aus dem laufenden Betrieb Abhilfe schaffen. Über den Datenraum Antrieb 4.0 können exemplarisch Metadaten abgerufen, nach Komponenten oder Maschinen und Anlagen gefiltert und der Zugriff auf Betriebs- oder Energiedaten beim Betreiber angefragt werden.
Das „Digitalisierte Asset Management“ hilft also dabei, Komponenten hinsichtlich ihrer Qualität und Energieeffizienz weiter zu optimieren, Simulationen zu verbessern und Komponenten optimal zu dimensionieren. Gleichzeitig werden im Entwicklungsprozess Zeit, Kosten und Ressourcen reduziert.
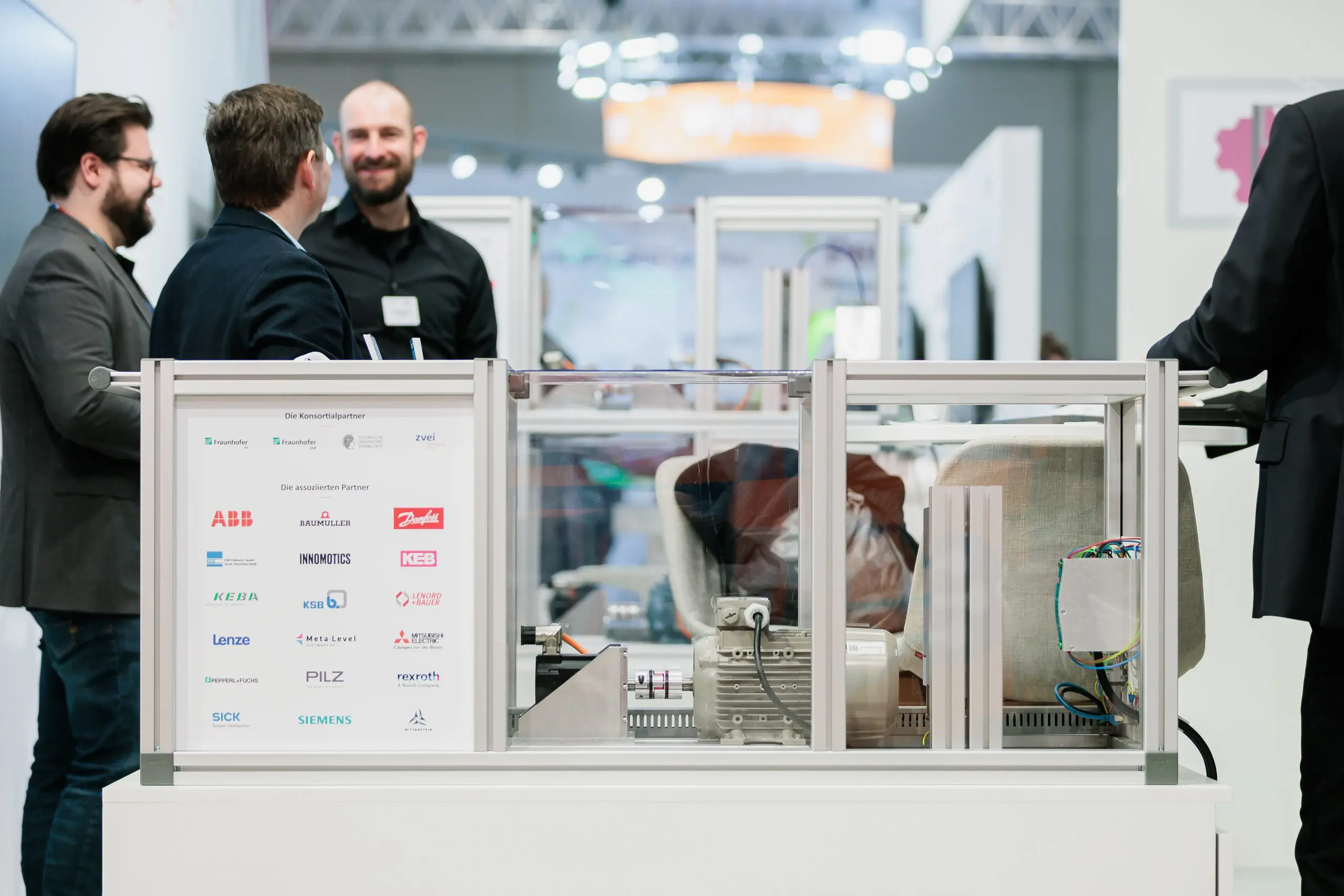
Wo liegen die Vorteile des souveränen multilateralen Datenteilens?
Diese und weitere Fragen diskutierte der Forschungsverbund im Rahmen von drei Veranstaltungen auf der All Electric Society-Arena und der Conference Stage Industrie 4.0.
Tomás López Mendez (Fraunhofer IIS) war sich sicher, dass eine verbesserte Interoperabilität eine Vielzahl neuer digitaler Dienstleistungen ermöglichen wird. Während Endanwender von einer gesteigerten Gesamteffizienz und Zuverlässigkeit von Antriebssystemen profitieren, werden weitere kooperative Geschäftsmodelle einen erheblichen Beitrag zur Umsetzung einer Smart Circular Econmy leisten. Auch Lara Schmidt (Fraunhofer IIS) unterstrich in der Paneldiskussion, dass sich im Ökosystem Antrieb 4.0 Geschäftsmodelle durch gesteigerte Interoperabilität und gemeinsame Standards grundlegend verändern werden. Die Entwicklung und Nutzung digitaler Services wird herstellerübergreifend ermöglicht und dadurch skalierbarer, wodurch Unternehmen im Ökosystem nicht nur ihre ökonomische Performance verbessern, sondern auch die Umsetzung einer zirkulären Wirtschaft vorantreiben können. Dies führt zu einer erhöhten Resilienz und Innovationskraft.
Trotz der Vorteile sind die Hemmnisse für Unternehmen noch hoch. Diese liegen nach Meinung von Dr. Jan Hofmann ( Fraunhofer IIS) in der immer noch unklaren Anreizsituation für das multilaterale Datenteilen. Und die technische Seite stellt leider oftmals einen kleinsten gemeinsamen Nenner verschiedener Strömungen dar. Hier müssen leichtgewichtige Lösungen her, die je nach Anwendungsfall schrittweise erweiterbar sind.
Michael Klipphahn (ABB) erklärte, dass das „Digitalisierte Asset Management“ einen effizienten und unmissverständlichen Informationsaustausch ermögliche, der den manuellen Aufwand erheblich reduziert. Es schafft damit auch die Grundlage für zukünftige Anwendungen der Künstlichen Intelligenz, indem es präzise und zuverlässige Daten bereitstellt. Bernd Wacker (Siemens) ergänzte, das mit dem Use Case Asset-Daten beteiligter Maschinen und Geräte im Produktionsprozess direkt online gelesen und ausgewertet werden können. Das spart an Zeit bei Online-Prozessen wie Energieoptimierung oder aber auch bei Offline-Prozessen wie Engineering, Reparatur und Beschaffung.
Für Stefan Pollmeier (ESR Pollmeier) liegt das Erfolgsrezept eines offenen Standards in dem offenen Standard Verwaltungsschale, aka AAS. Damit haben die Antriebsanwender im Maschinenbau und den Fabriken eine solide interoperable Basis. Auch Antrieb 4.0 baut darauf auf.
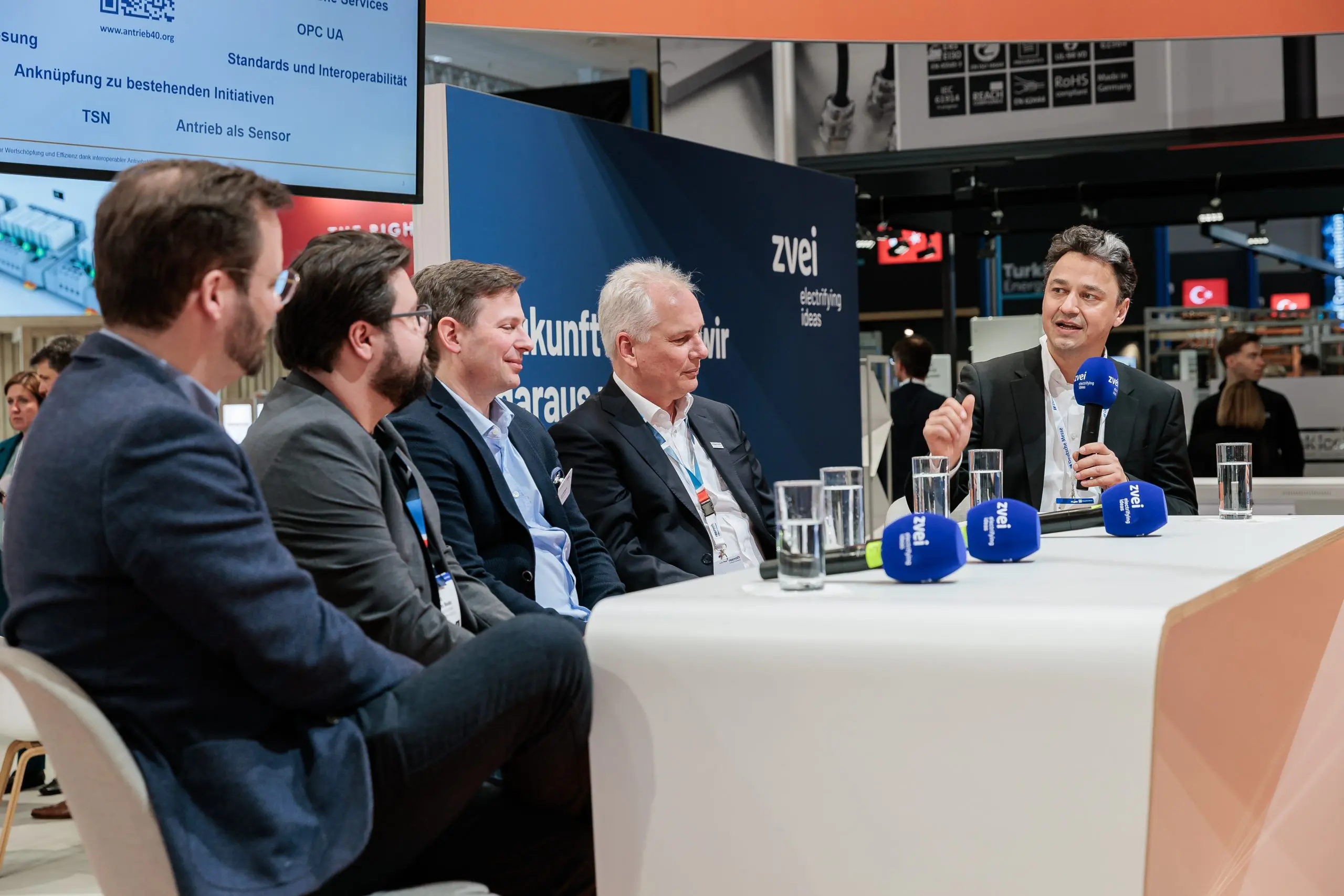
Wie das multilaterale Datenteilen in Zukunft aussehen könnte, hat die Antrieb 4.0-Systemarchitektur auf der Hannover Messe veranschaulicht. Sie ermöglicht eine vertikale Vernetzung vom Feld über die Edge in die Cloud mit Zugriffsberechtigungen für beteiligte Akteure wie den Betreiber, den Antriebshersteller oder den Maschinen -und Anlagenbauer. Mit einer entsprechenden Authentifizierung können den verschiedenen Nutzergruppen über den Datenraum und Verwaltungsschalen (Asset Administration Shells, AAS) benötigte Daten auch horizontal für eine definierte Nutzungsart und Dauer zur Verfügung gestellt werden. Durch den einfachen Zugriff auf der in einer Anlage verbauten Antriebe und Komponenten kann in Zukunft im laufenden Betrieb die Transparenz in der Fabrikhalle hergestellt werden.