Ein reges Messetreiben herrschte am Stand des ZVEI e.V.. Dort präsentierte der Forschungsverbund erste interoperable Projektergebnisse am Beispiel des Energiemonitorings. Es wurde deutlich, dass sich mit Hilfe des multilateralen Datenteilens die Effizienz, die Nachhaltigkeit und die Kosten im laufenden Betrieb zukünftig erheblich verbessern lassen. Ein Demonstrator veranschaulichte dafür die möglichen Wege der vertikalen Vernetzung eines Antriebs über die Produktionsanlage bis hin zu weiteren Hierarchieebenen im Fertigungsbereich auf.
Erste Umsetzungen der herstellerunabhängigen und einheitlichen Datenbereitstellung in einem Datenraum „Antrieb 4.0”
Antrieb 4.0 forscht im Use Case „Ganzheitliche energieeffiziente Auslegung von Antriebslösungen“ an der Möglichkeit für Anlagenhersteller, Antriebssysteme für ein vom Betreiber vorgegebenes Last- und Bewegungsprofil durch die Kombination von Antriebskomponenten unterschiedlicher Hersteller möglichst energieeffizient auszulegen. Für den Teilaspekt des Energiemonitorings wird es nun mit einer entsprechenden Authentifizierung möglich, über einen Datenraum die tatsächlich bezogene Leistung und den kumulierten Energieverbrauch aller in einer Anlage verbauten Antriebe in einem bestimmten Zeitfenster einzusehen. Die Energieverbräuche können für die ausgewählte Konfiguration des Antriebssystems prognostiziert und während der Inbetriebnahme verifiziert werden. Dies erleichtert eine übersichtliche und effiziente Auslastung der Anlage und trägt zu einer längeren Lebensdauer des verbauten Systems bei. Zudem können die tatsächlich erfassten Ist-Werte zwischen Betreiber, Maschinenbauer und Anlagenhersteller ausgetauscht werden. Dies kann Hinweise auf Optimierungen im Fahrprofil einer Anlage geben.
Welche technischen Herausforderungen dahinterstecken
Im Vortrag „Antrieb 4.0 Ökosystem: Technische Herausforderungen der Skalierbarkeit und Implementierung“ der beiden Referenten Dr. – Ing. Michael Wolff (TU Darmstadt) und Dr. Jan Hofmann (Fraunhofer IIS) auf der Technology Stage powered bei ZVEI/VDMA wurde deutlich, dass eine wesentliche Herausforderung in dem Thema Datensouveränität lag. Denn die Daten sollen genau dort bleiben, wo sie entstehen. Aus diesem Grund hat sich der Forschungsverbund für den Aufbau eines dezentralen Datenraums entschieden, der ein Webportal inklusive Daten- und Servicekatalog für den Datenraumnutzer beinhaltet. Ein globaler Solid-Server orchestriert die Anfragen der einzelnen lokalen Bestandteile an die Edges. Der Dateneigentümer kann so die Daten freigeben oder bei Bedarf den Zugriff sperren. Im Feld sind die Antriebssysteme und damit die Datenquellen verortet. Dort werden die dynamischen Antriebsdaten erhoben. Das System musste nun so umgesetzt werden, dass eine solide und zuverlässige Nutzung der Daten gewährleistet werden kann.
Auf der SPS veranschaulichte der Demonstrator die Wege der vertikalen Vernetzung vom Feld über die Edge in die Cloud mit Zugriffsberechtigungen für die verschiedenen Akteure. Zunächst kann sich der Anlagenbetreiber an der Edge einloggen und den Motor über den OPC UA-Client eines bestimmten Antriebssystems zu einem gewünschten Zeitpunkt starten und stoppen. In dieser Zeit werden wichtige Daten des Motors im Feld generiert und ausschließlich lokal in der Datenbank der Edge gespeichert. Darauf aufbauend können die generierten Daten nun über den Datenraum „Antrieb 4.0” weiteren berechtigten Instanzen für eine definierte Nutzungsart- und -dauer zur Verfügung gestellt werden. Mit einer entsprechenden Authentifizierung an der Cloud kann sich beispielsweise der Antriebshersteller im Datenraum einloggen. Dort erhält er Zugriff auf die Daten der in der Anlage verbauten Antriebe und Komponenten, die während des Betriebs gesammelt wurden. Somit kann er Rückschlüsse auf den Energieverbrauch, die Energieeffizienz und mögliche Optimierungspotentiale aus der Anlage ziehen. Der physische Demonstrator zeigt Antriebssysteme verschiedener Hersteller, die standortübergreifend miteinander kommunizieren können.
Und wie wurde die Interoperabilität erreicht?
Eine interoperable Lösung wurde durch die Übersetzung der vielen proprietären Feldbussysteme in ein OPC UA- System geschaffen. Damit konnte eine einheitliche Schnittstelle erreicht und bei der Umsetzung alle Interessensgruppen der Fertigungsindustrie, Prozessindustrie, die eventuell auf unterschiedliche Spezifikationen zurückgreifen, bedacht werden. Der Verbund hat sich für ECLASS und Spezifikationen von der OPC UA-Foundation entschieden. Der Schlüssel zu allen Anforderungen lag und liegt im starken Konsortium von Antrieb 4.0. Im direkten Austausch mit den Konsortial- und assoziierten Partnern konnte iterativ der Prozess immer weiter verfeinert werden, bis der technologische Durchstich gelungen ist.
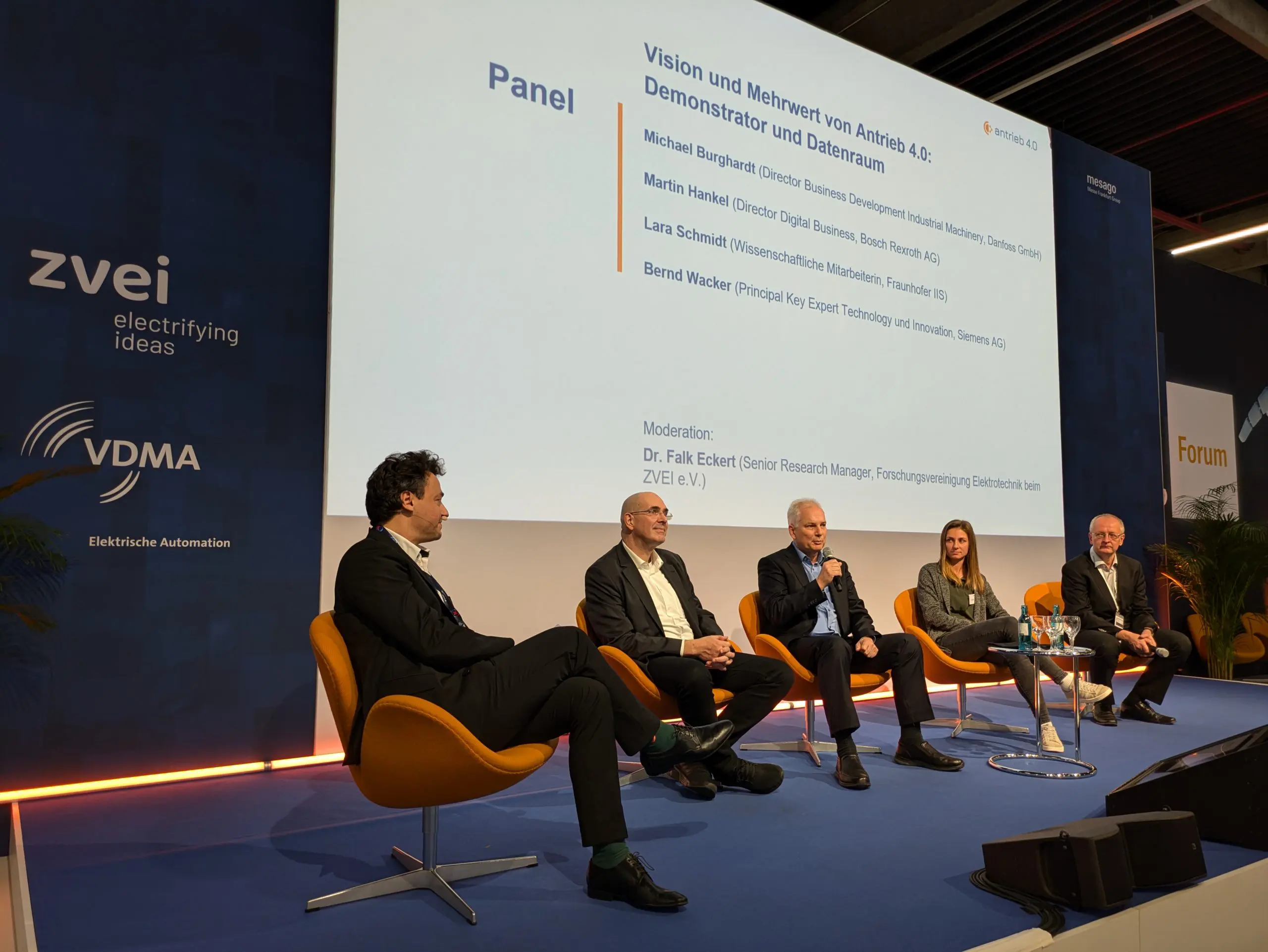
Das multilaterale Datenteilen bietet viele Chancen für die Industrie
Das war einer von vielen Punkten in der Antrieb 4.0-Panel-Runde zum Thema „Mission und Mehrwert von Antrieb 4.0: Demonstrator und Datenraum“. Die Gesprächsrunde bestehend aus Michael Burghardt (Danfoss GmbH/Drives), Martin Hankel (Bosch Rexroth), Lara Schmidt (Fraunhofer IIS) und Bernd Wacker (Siemens AG) war sich einig, dass das multilaterale Datenteilen viele Mehrwerte für Kunden und Hersteller bieten kann und es Zeit wird, die Chancen mehr in den Fokus zu stellen. Der Use Case „Ganzheitliche energieeffiziente Auslegung von Antriebslösungen“ zeigt der Industrie unter anderem, wie der Energieverbrauch optimiert, der CO2-Gehalt eingespart und die Wettbewerbsfähigkeit gesteigert werden kann.
Warum es bislang noch keinen Durchbruch in der Industrie 4.0 gegeben hat, wurde mit dem imaginären Blick in eine Industriehalle deutlich. Dort stehen circa 100 Maschinen. Jede Maschine umfasst mindestens zehn Antriebe und 1000 Assets. Ein Asset hat mindestens 250 Merkmale, das heißt in der Fabrikhalle existieren an den verschiedenen Maschinen ungefähr eine viertel Million Merkmale. Ein harmonisiertes Datenmanagement mit ECLASS-Merkmalen und OPC UA-Schnittstellen ist im Brownfield, also in einer bestehenden Fabrik sehr aufwändig. Im Greenfield, einer neu geplanten Fabrik, lassen sich die interoperablen und standardisierten Lösungen leichter integrieren. Antrieb 4.0 setzt auch hier an und forscht, welche Grundlagen und Merkmale es rund um die digitalisierte Produktion und vernetzte Wertschöpfungskette braucht und wie sich daraus serviceorientierte Geschäftsmodelle entwickeln lassen.